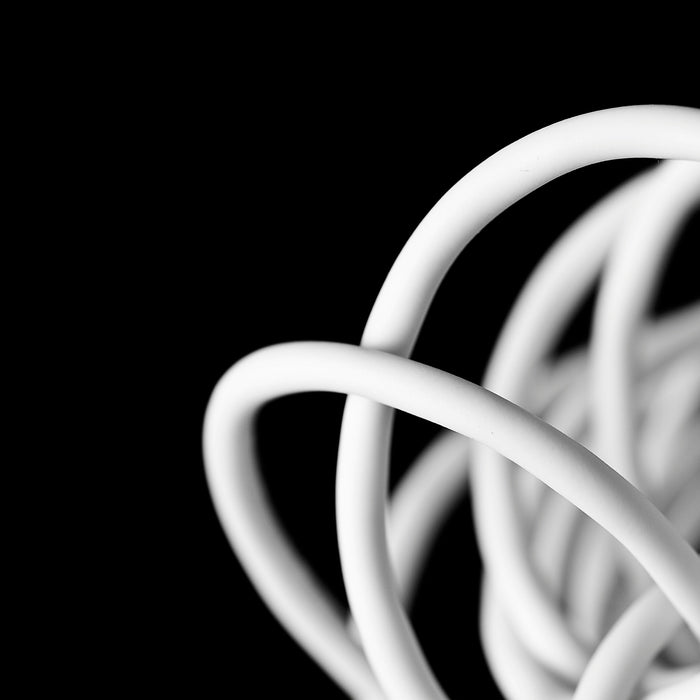
Multi-Conductor Cable Types
You know you want to use multi-conductor cables because they streamline complex wiring, ensure reliable signal transmission, and are customizable to fit a vast array of applications. The only question is, which of the multi-conductor cable types is right for...